【コラム】アドバンテージ流 Z系改造論 #02(サスペンション編)
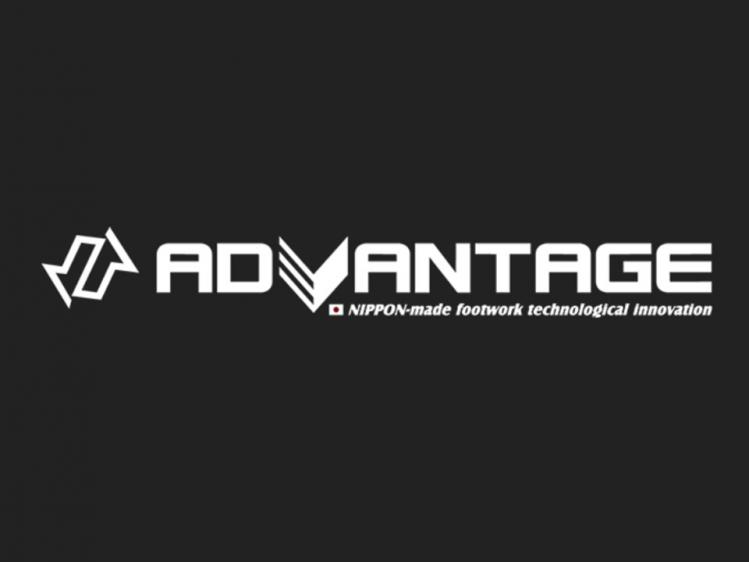
ADVANTAGE(アドバンテージ)のブログ
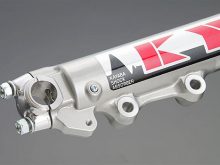
“Z系のサスペンションを現代の技術で蘇らせる”。今回はADVANTAGE KYBで旧カワサキワークスの復刻を目指してきたお話です。
まずサスペンションの中身をリニューアルする必要があるのですが、当時に比べたら現代の基準は何もかもがバージョンアップされており、狙い通りの性能を確保するには相当な時間と労力が必要でした。
図面自体は当時の手書きによるものですが、現在はCADです。これらは理屈抜きに大変な労力を要します。ディテールは非常に重要ですから、当時のカワサキワークスと同じデザインで、全てを設計し直します。各アールの付き方等どうしてもCADで描くとシャープになってしまいます。設計は以前よりも遥かに精度が高く、無駄な肉も付きにくいため、見た目が変わってきてしまうのです。
金型技術も遥かに向上しており、方式も違うため、加工公差の設定や安全率に関しても、改めて設定し直す必要があります。現在の製品開発は過去の公差、安全率が以前とは明らかに違い過ぎるのです。40年前のパーツを再生産するなら、当然そのままで安全率はクリアということで良いと思うのですが、そこはさすがKYB。最新の安全率や公差範囲でないと製品化出来ません。つまり当時のデザインそのままでは、製品化をあきらめてくださいと言うようなものです。
デザイン(意匠)はアイデンティティーですから、絶対譲れません。特に困ったのはアウターチューブとインナーチューブです。現在のアウターチューブはデザイン的に真円を採用していますが、当時は楕円形が主流でした。これが内径公差を厳しくしているのです。楕円形状のアウターチューブに対して真円のフォークの厳しい公差を守れとなると、もう至難の業です。しかし製品化にあたり、それらをクリアしないとO.K.は頂けません。
そこで行ったテストは、アウターチューブ100台分をあらゆる方法で加工し、公差範囲を設定するというものでした。これはとてつもなくお金や時間がかかる方法で、それによって導き出した工法と公差で製品の試作が始まりました。
このように国内での製品化や、国内のトップメーカーで製品化するということが、お金の面で見合うのか? 納期に間に合うのか? と言うと、はっきり言いって難しいと思います。試作を1本作るのも1万本製品化するのも、同じ規格が適応されるのです。この事が、日本製のカスタムパーツが極めて少ない原因と言えるのです。しかしながら我々は日本製品にこだわり、製品化を続けています。それだけの価値が、そこにはあるのですから。